RUBBER
- PRODUCERS
Please use our A-Z INDEX
to navigate this site or see HOME
STORED
ENERGY - A
different way of looking at a pile of worn tyres, is that they
are a resource that might be effectively recycled, if designed
differently, for a cradle to grave system. Otherwise we might
go back to horse drawn carriages and mud tracks. Slow and
uncomfortable, but a whole lot more healthy, apart from the
horses passing wind and leaving organic deposits as they go.
Realistically,
we
cannot do without rubber tires for our vehicles, or soles
for our shoes. Tires (or tyres) are
essential to modern living and the right to mobility, to get to
work
and do the shopping, or attend the doctor. Tyres are the cornerstone of goods deliveries from
docks, factories and farms, to retailers, and thence to your door. It is
pointless going over to clean electricity for propulsion, to
eliminate exhaust pollution, if we don't tackle road dust in
air.
There
is nothing wrong with rubber if we start to treat the
technology with the respect it deserves. And that is a bottom
up re-think of how to stop the black mud from infecting the
ocean and fine particles from entering our
lungs.
Tyre wear is the second-largest microplastic pollutant in our ocean after single-use plastic and accounts for up to 50% of air particulate emission (PM) from road transport. Tyres wear out from friction every time we brake, accelerate or turn a corner. The particles become airborne affecting our lungs. More are swept into our waterways and oceans eventually entering our food chain.
Tyres are actually among the most common plastic polluters on earth. A 2017 study by Pieter Jan Kole at The Open University of The Netherlands, published in the International Journal of Environmental Research and Public Health, estimated that tyres account for as much as 10 percent of overall microplastic waste in the world’s oceans. A 2017 report by the International Union for Conservation of Nature put that number at 28 percent.
The No. 9 London bus, on average releases 4.65g per journey and a total of 65g a day. Car and EV quantities based on a 16km UK average commute per day.
Who'd want to live in a city, knowing about brake and tyre
dust and diesel
particulates?
A 2013 report by Tyre Steward Manitoba, in Canada, found that passenger light
truck tyres lost nearly 2.5 pounds of rubber during their service life (average of 6.33 years). The Kohl study found that Americans produce the most tyre wear per capita and estimates that, overall, tyres in the U.S. alone produce about 1.8 million tons of microplastics each year.
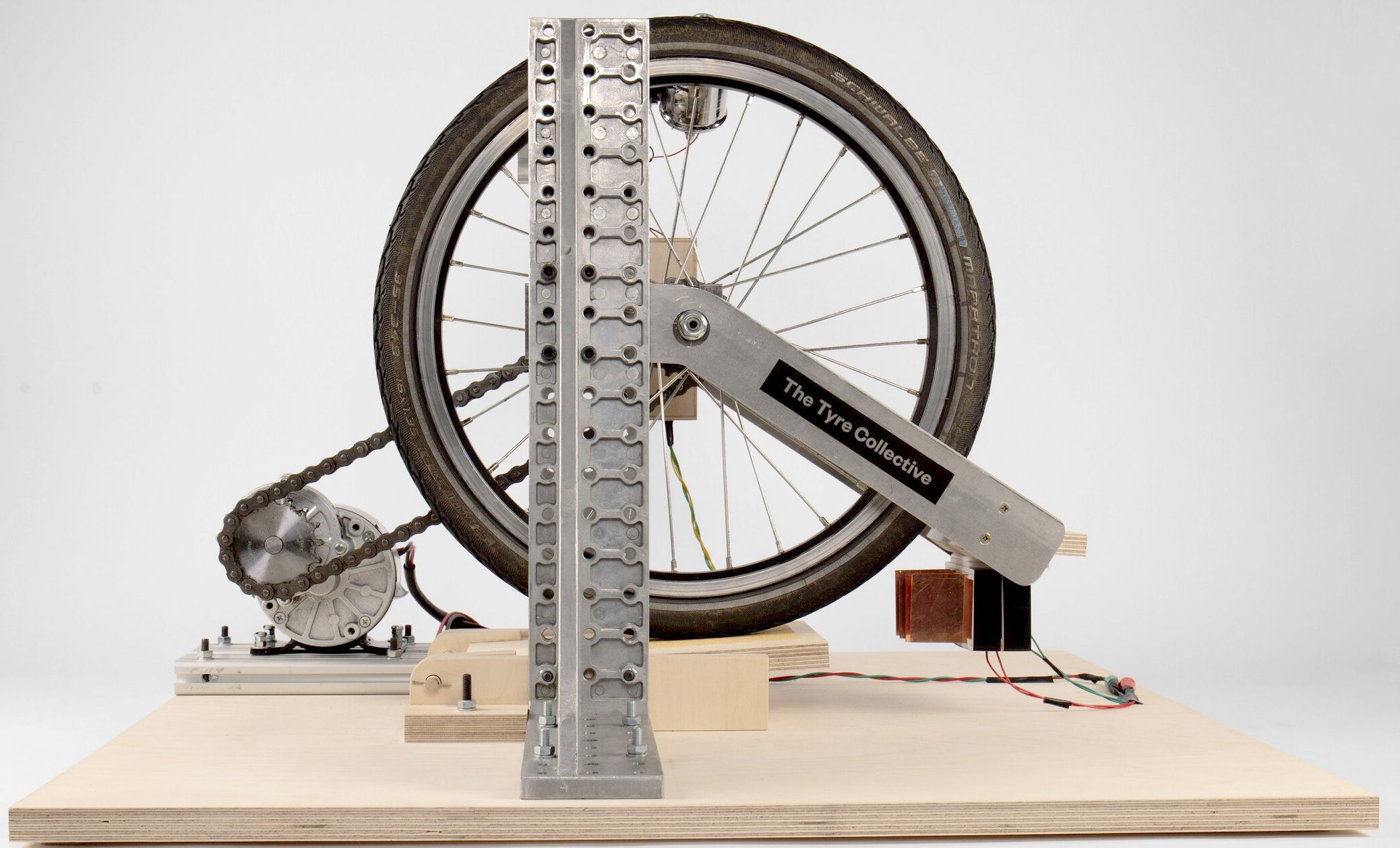
WHEEL
INVENTION - As
a natural development from logs, used by the ancients to move
giant rocks and build pyramids, to wooden wagon wheels,
pneumatic tyres were invented by Dunlop, paving the way for
tarmac and concrete roads. Great news for those who want a
comfortable ride, not so great for your lungs and marine life.
THE TYRE COLLECTIVE
The carbon in rubber particles is charged as they tear off of the tyre.
You may have seen this effect at parties when rubbing a balloon against a
sweater and sticking it to the ceiling. This observation eventually led to
an air
scoop that directs and captures charged tyre particles to a
collector, so reducing release into the air by over 50%.
Particles under 50 microns are small enough to be reused in new tyre walls, and other
applications, so is good news for recycling.
The device is positioned close to where the tyre meets the road. Consulting with the Imperial Department of Aeronautics
the innovators identified the best position to take advantage of airflow around a spinning
wheel experiment. Their device currently captures a claimed 60% of all airborne particles on
their test rig.
Once tyre particles have made it into rivers or
oceans, they can have noticeable effects on marine life. John Weinstein, at the Citadel, exposed shrimp to tyre particles in lab settings and found that the animals ate the particles, which also got stuck in their gills. Once ingested, particles balled up in the shrimp’s guts.
There are these chronic long-term effects that really haven't been studied.”
USED TYRES DISPOSAL
The trajectory for used tyres is, in many ways, positive. For example, the recycling of tyre scraps into products such as playgrounds, sports fields, and building materials has increased dramatically over the years. The U.S. Tyre Manufacturers Association (USTMA) says the re-use of tyres has gone from 11 percent in 1990 to 81 percent in 2017.
According to Reto Gieré, an environmental scientist at the University of Pennsylvania, if tyres are burned in facilities specifically designed for the task, it can be done fairly cleanly and is a decent way to recapture energy.
Tyres that aren’t recycled or burned mostly end up in landfills
- some 16 percent, according to a 2018 USTMA report. The amount of landfill-disposed tyres per year nearly doubled between 2013 and 2017. John Sheerin of USTMA told Recycling Today magazine that, with demand for tyre derived fuels in a decline, even more tyres could start heading toward landfills.
REDESIGN
In 2017, researchers led by the University of Minnesota found a way to produce isoprene, a key ingredient in synthetic rubber, out of natural sources such as grass, trees and corn instead of fossil fuels. In 2018 Goodyear unveiled a concept tyre made from recycled rubber that has moss in the middle, which is designed to soak up
carbon dioxide as it travels.
Reducing tyre wear, the Kole study says, would likely come at the cost of other performance metrics, such as
decreased grip, but also reduced rolling resistance, a tradeoff that may prove difficult for manufacturers to
accept, and especially challenging for motor sports where fast
cornering demands extra grippy (softer) compounds that wear
much quicker.
Road surfaces, could be made less abrasive or more porous to either reduce or help collect tyre wear particles.
There is room for better technology to capture tyre particle runoff from roads.
Overall, though, what is needed is urgent further research and increased scientific and public awareness.
Could there be an alternative to rubber/plastic based tyres?
The
scientists working for rubber companies should be looking for
a synthetic rubber compound that breaks down in water. This
allied to compulsory air scoops for trucks and buses and
perhaps other (mass) devices in cities to filter air, such as
in offices and public buildings, might help to reduce lung
related illnesses such as cancer.
We've
all come home from visiting a city, to find our collars and
noses lined with black residue. The human nose is not an
effective filter to protect the lungs. The better masks used
for Covid, may help to reduce inhalation of damaging
particles.
GIVING
CONSUMERS AN INFORMED CHOICE
1. Test and label tyres
At the moment there are European tyre labelling regulations covering things like wet grip, noise, and fuel consumption, but not wear and tear. The present rules should include a requirment to make it clear how resistant each type of tyre is to wear and tear.
There should be clear labeling of such performance features that buyers might readily understand.
2. Capture tyre pollution from roads
Existing roads might have their drains cleared more often. For
new roads more efficient use of roadside gully pots could be
made – where they are used to catch debris, sediment and microplastics before they get into the drains or waterways.
Such capture devices can be up to 80% effective if they are emptied regularly, but unfortunately they
are allowed to overfill and overflow.
Porous asphalt, though more expensive can help trap tyre particles in the road surface
for when cleaning is scheduled. It’s also known to be a safer road surface for drivers, as it reduces standing water and
spray.
3. Better road cleaning and geo data
Road sweeping can be used to mop up tyre particles from the roads or adjacent paths. Scheduling is important for this, as it’s best done just before it rains. The UK also has detailed traffic data which a local authority can use to target the busiest roads in the most effective way.
4. Incentives not to drive
There should be financial incentives not to drive, reflected in reduced insurance premiums and lower vehicle excise duty for users who drive less than
1,000 miles (19 miles per week) and then 3,000 miles (58 miles
per week), on a sliding scale up to the 10,000 miles, after which the full duty is payable.
HOW INDUSTRY CAN HELP
1. Make tyres more resilient to wear and tear
At the moment there’s no meaningful incentive for tyre manufactures to prolong the life of their tyres,
i.e. reduce the wear rate of the tread.
The European Tyre Manufactures Association (ETRMA) says that driver behaviour has the biggest effect on tyre wear, and that may be an issue. But that doesn’t change the fact that better wear characteristics in the tyre design will reduce microplastic
pollution, taking control of the situation and removing
behavioral delinquency from bad drivers.
It is common sense that with reduced wear rates that tyre grip and therefore safety, may become an issue. Nevertheless, manufacturers can and do make tyres that grip well and have better wear qualities.
Manufacturers should prioritize the development of tyres that maintain or improve performance in terms of efficiency and handling, and reducing the rate at which the tyre tread wears.
2. Alternative tyre materials
The tyre manufacturing industry has apparently been working on biodegradable polymers for many years, although there’s nothing commercially available so far.
One of the big challenges is to find a material that biodegrades safely and effectively in the environment, but is tough enough not to disintegrate too easily or quickly in everyday use.
Michelin has proposed an airless tyre that can be 3D printed from organic material and is fully biodegradable.
3. Retail buyers guide
In the UK alone around 50 million tyres are sold every year. But tyres aren’t a frequent purchase for most people, meaning that buyers generally don’t know enough about them.
Retailers should actively support a tyre-wear-rate labeling scheme, and help explain the options at the point of purchase.
Research shows us that consumers already find the concept of mileage (how many miles the tyre will last) to be equally as important as the tyre’s effect on fuel efficiency.
Hence, so-called eco tyres. Many of which are actually
beneficial to the environment.
Key Players featuring in
tyre market:
Michelin, Clermont-Ferrand, France
Bridgestone, Kurume, Fukuoka, Japan
Continental AG, Germany
Goodyear Tire & Rubber Company, Akron, Ohio, USA
Pirelli, Milan, Italy
Yokohama Tire Corporation, Tokyo
Sumitomo Rubber Industries, Japan (Dunlop)
Hankook Tire Group, Seoul, South Korean
Toyo Tire & Rubber, Toyota, Japan
Kumho Tire Co., Gwangju, South Korea
Giti, Singapore, Inodnesia
MRF Madras Rubber Factory, India
Cooper, Tyre and Rubber Company, America (motorcycles)
Maxis, Cheng Shin Rubber
CST Cheng Shin Rubber Ind Co Ltd (bicycle)
Huayi, Shaghai, China
Apollo, Gurgaon, Haryana, India
Nokian, Finland
Nexen Tire Corporation
IT'S
NOT RUBBER - Although we loosely call them ‘rubber’, vehicle tyres are actually made from a complex blend of a lot of mostly synthetic materials and chemicals, including different types of plastic.
It’s estimated that an astonishing half a million tonnes of tyre-wear fragments are released every year across Europe. The UK’s share of that is around 68,000 tonnes with up to 19,000 tonnes of microplastic tyre pollution getting into our waterways, rivers and seas each year.
Natural rubber may be a minor component (sometimes as little as 20%), but the bulk of a modern tyre is a mix of synthetic compounds, fillers, binders, plasticisers and other chemical additives to add strength, weatherproofness etc. The exact composition will vary and is often kept secret by tyre manufacturers.
One important but less-than-obvious ingredient added to tyres is carbon black. It’s a dark sooty material usually sourced from burning fossil fuels, and is used to increase tyre strength and resistance to UV light. It’s the main reason tyres are black.
Before carbon black was introduced, over 100 years ago, tyres were usually creamy white – the colour of natural latex. Carbon black is known not to be biodegradable, and is a ‘possible human carcinogen’, according to a report published by the International Agency for Research on Cancer.
According to government figures, there are around 30 million cars licensed for use in the UK. That means 120 million car tyres on our roads. And that’s not including all the lorries and massive multi-wheeled HGVs, from the UK and elsewhere, that thunder down our streets and motorways every day. All that rubber on the road is potential plastic pollution down the drain.
Modern tyres include a variety of synthetic polymers, with names like styrene butadiene and halobutyl rubber, and polyester cord fibres to strengthen the internal structure. In short, tyres are essentially yet more big chunks of plastic. And when they break down they behave and persist like other plastics in the environment.
Once in the ocean, tyre particles absorb and concentrate toxic pollutants from seawater, like other microplastics do. This makes them even more poisonous to animals that mistake them for food or absorb them through their gills or skin.
Airborne microparticles (and even smaller nanoparticles) are a worry on land too. It is estimated that up to 10% of tyre wear is generated as airborne particles, which contribute to ongoing problems of air pollution and lung problems in UK cities.
RUBBER
COMPANY
|
EMPLOYEES
|
$
BILLIONS
|
-
|
-
|
- |
Michelin
|
-
|
- |
Bridgestone
|
-
|
- |
Continental
|
-
|
- |
Goodyear
|
-
|
- |
Sumitomo
|
-
|
- |
Pirelli
|
-
|
- |
Yokohama
|
-
|
- |
Hankook
|
-
|
- |
Toyo
|
-
|
- |
Kumho
|
-
|
-
|
Giti
|
-
|
-
|
MRF
|
-
|
-
|
Cooper
|
-
|
- |
Maxxis
|
-
|
- |
CST
|
-
|
- |
Huayi
|
-
|
- |
Dunlop
|
-
|
- |
Apollo
|
-
|
- |
Nokian
|
-
|
- |
Nexen
|
-
|
- |
*
WHAT CAN YOU DO?
1. Choose to walk, cycle or share vehicles
Walking or cycling is a preferred solution, but not everyone
can do it. Shared vehicle journeys would be the next best thing. There are
many car-sharing schemes you can find out about online.
2. Drive gently
When a journey by car is unavoidable, you can reduce tyre wear
by eco-driving:
- Drive smoothly and avoid aggressive manoeuvring and abrupt
cornering
- Accelerate
gently
-
Don't over-brake. Brake pad wear is another source of microplastic pollution
(dust) on the roads. Electric cars with regenerative braking
(nearly all) use the brakes far less.
- Drive with the correct tyre
pressure
- Remove unnecessary weight from the
vehicle
- Choose a smaller,
or lower-weight vehicle
Electric
cars generally have a lower rolling resistance from larger
diameter wheels (BMW
i3 example) or eco tyres, but they are still made of the
same synthetic rubber as conventional cars, so cause microplastic
pollution in some degree.
LINKS
& REFERENCE
https://qmotu.com/top-20-tyre-manufacturers/
https://friendsoftheearth.uk/sustainable-living/tyres-and-microplastics-time-reinvent-wheel
https://deframedia.blog.gov.uk/2019/07/11/air-pollution-from-tyres-and-brakes/
https://qmotu.com/top-20-tyre-manufacturers/
https://phys.org/news/2019-11-rubber-environment.html
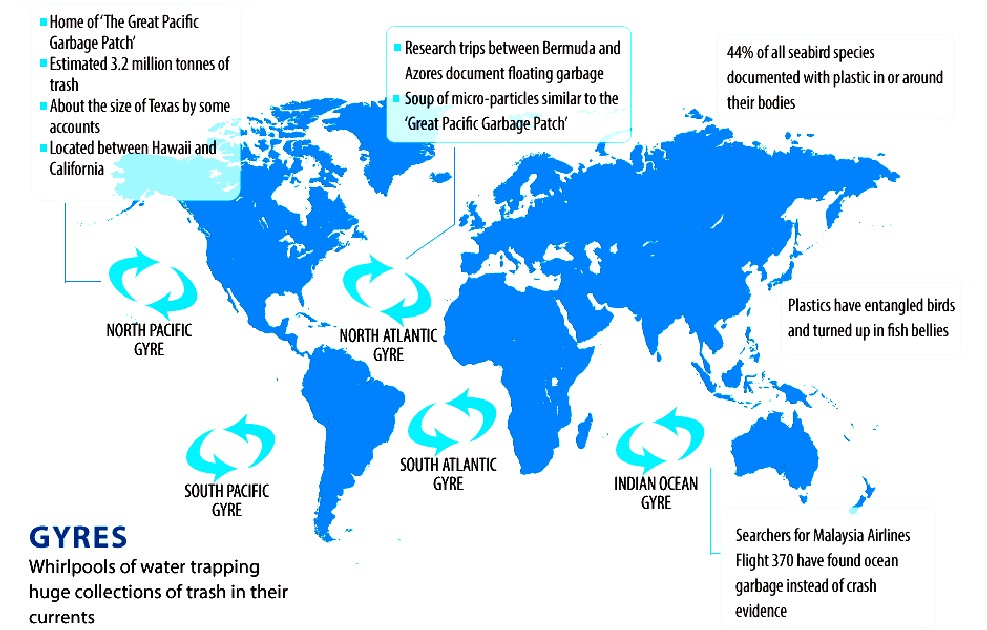
MARINE
LITTER BUILD
UP
-
Plastic has accumulated in five ocean hot spots called gyres, see here in this world map derived from information
published by 5 Gyres. All that plastic just floating around is a huge waste of resources in a sustainable sense, where we should be aiming for
a circular economy.
ABS
- BIOMAGNIFICATION
- CANCER
- CARRIER
BAGS - COTTON
BUDS - DDT
- FISHING
NETS
HEAVY
METALS - MARINE
LITTER - MICROBEADS
- MICRO
PLASTICS - NYLON
- PACKAGING
- PCBS
PET
- PLASTICS
- POLYCARBONATE
- POLYSTYRENE
- POLYPROPYLENE
-
POLYTHENE - POPS
PVC - SHOES
- SINGLE
USE - SOUP
- STRAWS
- WATER
PLEASE
USE OUR A-Z INDEX TO
NAVIGATE THIS SITE
This website is
provided on a free basis as a public information service. copyright © Cleaner
Oceans Foundation Ltd (COFL) (Company
No: 4674774) 2021.
Solar
Studios, BN271RF, United Kingdom.
COFL is
a company without share capital.
|